Metal fabrication produces an infinite array of items used in daily life. Just like the printing industry, a lot of raw materials, deep thought and machinery go into the creation of these indispensable everyday products.
Ask fabricators which services they handle in-house and which steps are outsourced. This will help you determine which fabricator best fits your project needs. Visit https://www.83metalcraftboise.com/ to learn more.
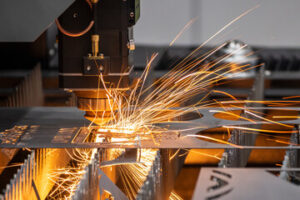
Whether they are laser cutting or waterjet sawing, shearing, or flame cutting, metal fabricators use these methods to transform raw sheets of metal into usable chunks. The size of these chunks depends on the dimensions and shape needed for the final product. For example, if a piece of metal must fit inside another, the fabricator may require precise concentricity or cylindricity. To make such measurements, a fabricator creates a part drawing that lists the desired characteristics with their +- tolerances.
Once the metal fabrication shop creates a drawing, they can start the cutting process using one of many technologies. For small pieces, the most popular is CNC (computer numerical control) milling. This technology uses computer software to program the movement of a blade or spindle through a part, which is then fed into the machine for machining.
This technology allows metal fabrication shops to produce accurate and consistent parts at high speeds. This is especially important for industrial manufacturing. It can also help reduce the time it takes to finish a project and the associated costs.
Some of the most common products that result from the metal fabrication industry are tools and home appliances. Indoor and outdoor hand tools that are produced through a metal fabrication process include scissors, X-ACTO knives, hammers, saws, and bush trimmers. Home appliances that are made by the metal fabrication industry include refrigerators, washing machines, dryers, ovens, and dishwashers. Metals like steel and aluminum are used for these devices.
A wide range of metal fabrication services is available for both large and small businesses. Look for a company that offers both custom and mass production capabilities, so you can get the exact parts you need for your project. The right company will be able to accommodate your needs and provide quality service.
When looking for a metal fabrication company, be sure to choose a trusted partner with years of experience in the industry. In addition to experience, you should choose a company that uses the latest in technology and has a knowledgeable staff. They should be able to answer your questions and explain their processes. You should also ask for customer referrals, as these will give you an idea of the company’s level of service.
Forming
If you were to create an encyclopedia on all of the commercial and industrial machines, products, parts and other objects that use metals for their production, it would be quite a long list. The fact is, we live in a world that relies on the various elements of metal fabrication for everything from transportation to energy. As a result, it’s important to keep up with the latest developments in this field and to learn all about the many different processes that make up metal fabrication.
One of the most basic steps in forming metals involves cutting. This is done to transform sheets of flat metal into the specific shapes that are required for a particular project. There are a variety of ways this can be accomplished, including using lasers, plasma torches and waterjet cutting.
Shearing is another way that metal fabricators work with raw materials. This technique involves a machine that pulls a raw material through a series of cutting blades to give it the desired shape. Forging is yet another process where metals are shaped by heating them and then pressing them to mold them into a specific form. Other machining techniques include punching, which is done with a set of turrets that stamp pre-designed patterns into the metal.
Another way that manufacturers work with raw materials is by painting and coating them in a specific color or finish. This allows them to meet the unique needs of their customers, and it also gives the product a more visually appealing look.
Robots are becoming increasingly common in metal fabrication shops, and they help to reduce the amount of time it takes skilled welders to complete projects. These machines are able to work nonstop, which is crucial in the industry because of the demanding nature of some welding tasks. They also help to increase the accuracy of the welds, which is important for creating strong and durable parts and structures.
Specialized metal fabrication companies offer a broad range of services to their clients, and they often specialize in certain industries. Some of these companies are well-known for their ability to handle large projects, such as wind towers. Others are known for their expertise in specific types of steel or for their high-quality customer service.
Welding
Welding is one of the most common metal fabrication applications. It involves fusing two different parts of metal directly together using heat, pressure or both. The resulting joint is known as a weldment, and it helps create everything from skyscrapers to cars and aircraft. There are many ways to weld metals, and they include spot welding, resistance welding, electron beam welding and arc welding. The type of weldment used will depend on the type and thickness of the parts being joined.
Welded joints must be strong enough to withstand the weight of whatever they are supporting. This is a critical aspect of any welding application, and it is why most metal fabricators are committed to using the best possible equipment. They are also always searching for ways to improve efficiency and reduce costs.
As a result, the industry is embracing automation and other Industry 4.0 technologies in a big way. Robots are now a common sight in metal fabrication plants, taking on tasks that once took skilled human welders hours to complete. They help speed up production, improve quality and keep the plant running smoothly.
One of the biggest challenges facing the metal fabrication industry is the labor shortage, with welders and other highly-skilled workers in short supply. The good news is that most companies are doing their part to address the problem by partnering with schools and community colleges to offer training programs. They are also investing in apprenticeships and on-the-job learning opportunities.
Another challenge is the price volatility of raw materials, particularly steel and aluminum. This can squeeze profits and devalue existing inventory. To mitigate this risk, metal fabricators are increasing efficiencies and working with their suppliers to get better terms.
There are also new trends that are helping the industry stay competitive and sustainable. For example, some companies are recycling metal scraps to make new parts, which cuts waste and saves energy. Others are buying greener machines that run on renewable energy sources. And, some are even utilizing artificial intelligence to design parts and find the most efficient manufacturing methods.
Finishing
The fabricated metal industry is a little like the printing business. The finished products produced by each seem to be everywhere – in office desks, laptops, tablet computers, cellphones, door latches and handles, screws and nails, faucets, hangers, and more. Just like the printing industry, a lot of raw materials, software, equipment and deep thought are required to make it all happen.
Many metal fabrication companies have found ways to improve their operations by reducing waste and using cleaner energy. One way is by recycling scrap pieces of metal instead of throwing them away, and the other is by incorporating renewable energies into their facilities. Both of these strategies reduce costs, and they also help protect the environment.
Specialized companies in the metal processing industry offer a variety of services, including customization, diverse material options, precision manufacturing, value-added services, quick turnaround times, quality assurance, and collaboration. These services help them provide customers with the best possible results.
Automation is another major trend in the metal fabrication industry, with CNC machines now able to follow complex patterns and create intricate parts with ease. However, this has caused a labor shortage, with skilled workers like machinists and welders in short supply. Some metal fabricators are looking to expand their operations outside the US to find new sources of labor, but this requires significant investment in training and infrastructure.
In order to maintain a competitive edge, metal fabrication companies must continue to develop and innovate their products. This is especially important when they are dealing with rapidly fluctuating material prices. When the price of raw metals goes up, it can squeeze profit margins and devalue existing inventory. To combat these fluctuations, metal fabricators are getting creative with their pricing and focusing on efficiency and value-added services.
In addition, they are turning to automation to increase productivity and accuracy. Robots are now common sights in metal fabrication shops, and they can do tasks that would otherwise take skilled human welders hours to complete. This is helping them produce more product in less time and at lower cost.